For over a century, Foxboro has stood as a beacon of innovation. Setting the industry…
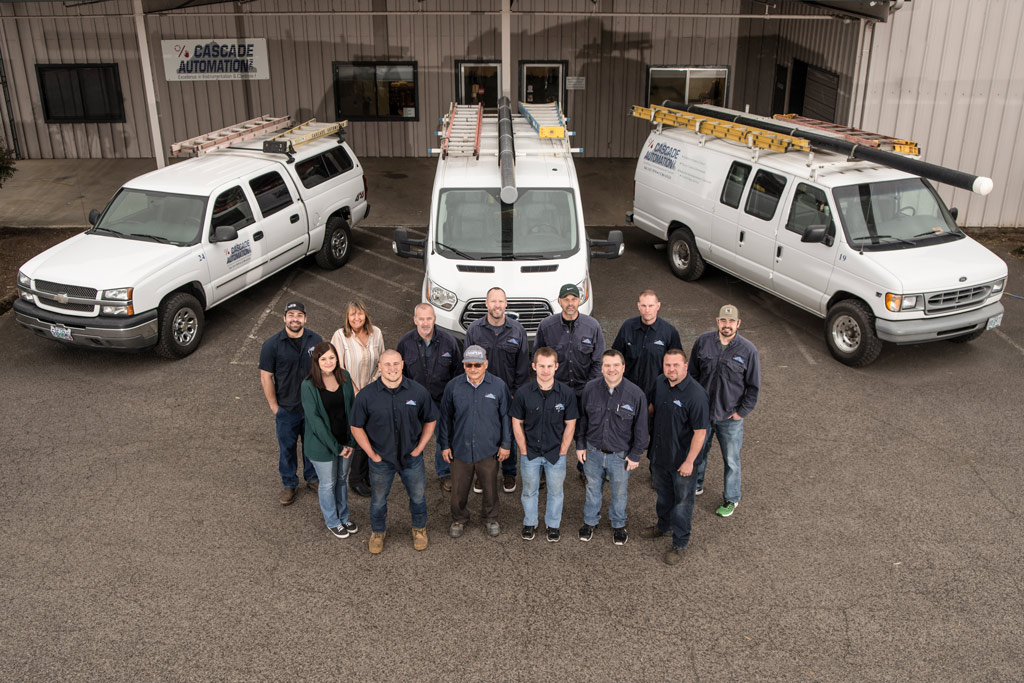
Mastering Precision: The Art of Onsite Instrument Calibration
In the intricate dance of industrial processes, precision is not just a goal; it’s an absolute necessity. The heartbeat of these processes relies on the accuracy of instruments, and the key to maintaining this accuracy lies in the art of onsite instrument calibration, particularly when adhering to NIST traceable standards.
The Foundation of Precision: NIST Traceable Calibration
National Institute of Standards and Technology (NIST) traceable calibration forms the bedrock of instrument precision. This renowned standard ensures that every measurement, every reading, and every output from an industrial instrument can be confidently traced back to the meticulously maintained standards of the NIST.
Understanding NIST Traceability: A Pillar of Confidence
At its core, NIST traceability means that the measurements recorded by an instrument can be directly linked to the NIST standards, which are recognized globally as the epitome of accuracy. When an instrument is NIST traceable, it instills confidence in the reliability of the data it produces. In the world of industrial operations, where accuracy can be the difference between success and failure, this confidence is invaluable.
Significance in Compliance and Quality Assurance
Compliance with industry standards and regulations is a critical aspect of many industrial operations. NIST traceable calibration provides a clear path to meeting these standards. Whether it’s ISO certifications, FDA compliance, or other industry-specific requirements, instruments calibrated to NIST traceable standards stand as a testament to an organization’s commitment to quality assurance.
The Calibration Process: Artistry in Precision
Onsite instrument calibration involves a meticulous process executed by skilled technicians. It’s not merely about adjusting the instrument to match a standard; it’s about understanding the unique characteristics of each instrument and fine-tuning it to deliver optimal performance.
Calibration Tools and Techniques: A Symphony of Precision
The technicians conducting onsite calibration employ a range of tools and techniques, each calibrated to NIST standards. These tools include precision calibrators, test weights, and other specialized equipment. The process often involves careful orchestration of adjustments to ensure every aspect of the instrument aligns with the NIST traceable standards.
Real-time Verification: Ensuring Continuous Accuracy
One of the significant advantages of onsite calibration is the ability to verify instrument accuracy in its actual operating environment. This real-time verification is crucial as it accounts for the specific conditions and variables the instrument encounters during regular operations.
Benefits Beyond Precision: A Holistic Approach
While the primary goal of onsite instrument calibration is precision, the benefits extend beyond accuracy alone.
Downtime Minimization: Keeping Operations in Tune
Onsite calibration minimizes downtime by eliminating the need to remove instruments from the production line. This efficiency is particularly valuable in industries where continuous operations are imperative.
Cost Efficiency: Investing in Long-Term Reliability
While investing in precision might seem like an added cost, it is, in fact, a long-term investment in reliability. Well-calibrated instruments are less prone to errors, reducing the likelihood of costly rework, product defects, or equipment damage.
In the grand symphony of industrial operations, where every instrument plays a crucial note, onsite instrument calibration is the conductor ensuring harmony. The art of calibration, especially when guided by NIST traceable standards, guarantees that the instruments remain in tune with the highest levels of accuracy. It’s not just about meeting standards; it’s about creating a melody of precision that resonates throughout the entire industrial process.